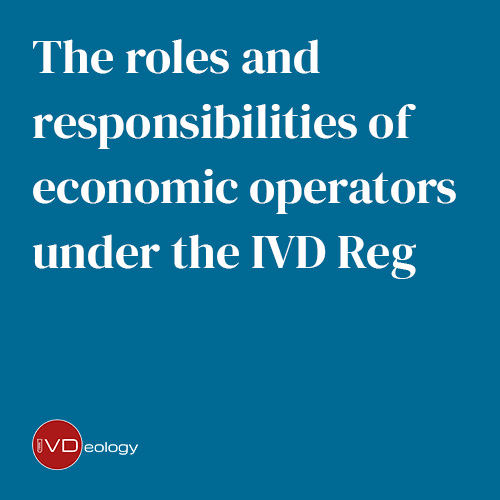
During the transition to the new IVD Regulation 2017/746/EU, manufacturers of in vitro diagnostic medical devices will need to include the understanding of the product distribution flow within their gap assessments to the new regulation.
The current IVD directive 98/79/EC details responsibilities for manufacturers, authorised representatives, importer and distributors. The new IVD Regulation which comes into force in May 2022 provides an update of those responsibilities.

Summary of Key Manufacturers Responsibilities
- Design and manufacture IVDs in accordance with requirements of the regulation
- Create and maintain a risk management file (ISO14971)
- Complete performance evaluation
- Compilation and maintenance of technical documentation and EU declaration of conformity
- Maintain an effective Quality Management System and undergo a conformity assessment (ISO13485) process
- Assign unique device identifiers (UDI) to applicable products and ensure all packaging and IFU requirements are met
Virtual manufacturers (formerly own brand labelling) who use third party providers to design and manufacture their products must now accept additional legal responsibility for the creation and maintenance of the product technical documentation and declaration of conformity. They must also maintain these documents within a quality management system which is subject to conformity assessment by a notified body.
Where the manufacturer is located in a third country outside the EU, they must appoint an Authorised Representative to act on their behalf within the EU for devices placed on the market.
Note: The requirement to establish an EU Authorised Representative may be applicable to UK manufacturers in the event of a ‘no deal’ Brexit arrangement.
Summary of key responsibilities of an Authorised Representative
- Ensure technical documentation and conformity assessment is completed by the manufacturer
- Hold current versions of the technical documentation and declaration of conformity
- Adhere to all product registration obligations
- Adhere to vigilance reporting obligations within the EU on behalf of the manufacturer
Both manufacturers and authorised representatives are required to appoint a person responsible for regulatory compliance, this person, or people, must have enough experience to assess the compliance of the device before being placed on the market. This includes reviewing the technical documentation and post market surveillance activities against the requirements of the manufacturers quality management system. The responsible persons are also responsible for the reporting and commination to the competent authorities of any vigilance activities related to the device within the EU.
Summary of key responsibilities of an importer
- Ensure that the device is in conformity to the regulation
- Ensure that the device is CE marked and registered (in Eudamed)
- Ensures that a declaration of conformity is available
- Checks that if an authorised representative is required, in appointed by the manufacturer and included within the packaging
- The device meets all labelling requirement of the regulation including IFU and assignment of a UDI
- Ensures that the packaging includes the importer name and address
- Maintains and monitors stability of the product throughout transport and storage
- Maintain and provide complaint and non-conformance data to the manufacturer
The importer is the first point of landing for devices that are manufactured in a third country. It is therefore important that the importer ensures that the products being received meet all the requirements of the regulation prior to distribution. The importer must be recognised within the packaging (IFU or label) and must have a process to collect, store and provide customer feedback to the manufacture as part of post market surveillance.
Summary of key responsibilities of a distributor
- Ensures that the device is CE marked and declaration of conformity is available
- Device is accompanied by an IFU
- Importer name and address is on the packaging
- A UDI is assigned
Distributors must establish a suitable sampling method to check that the incoming devices meet all the regulatory requirements. They must also maintain records of any customer feedback and provide it to the manufacturer.
If you are any of the above within the IVD market then it would be beneficial to talk to your suppliers/customers to ensure that the responsibilities for each are defined.
IVDeology Ltd can help IVD and Medical Device Manufacturers, Authorised Representatives, Importer and Distributors make an assessment of the responsibilities and provide support for all aspects of quality and regulatory compliance.
Please contact either Stuart or Nancy to find out more: [email protected]